The essential condition for an optimal design of a membrane or valve with a given function and specific applications is based on a close collaboration between the customer and EFFBE. This customer advice, specific to EFFBE and deeply anchored in its DNA, must begin from the first stage of the project, in order to best control deadlines and costs. This approach prior to the design of membranes or valves has been common practice since the creation of EFFBE in 1949.
The development of membranes and valves by EFFBE is carried out according to a 7-step process described below.
As your project develops, your EFFBE contact will mobilize and coordinate all the necessary internal key resources. It notably implements skills in engineering, prototyping, materials formulation and functional testing. This targeted project coordination helps ensure joint project goal achievement.
CO-DEVELOP YOUR PROJECT IN 7 STEPS
LISTEN TO AND INTEGRATE YOUR SPECIFIC NEEDS
To ensure the quality of our parts and services, EFFBE is committed to developing its products in partnership with its customers and to adapting or designing them according to mechanical, chemical and dimensional constraints.
An initial phase of listening to your needs & discussing your expectations is essential for validation of your specifications. This work is produced taking into account the performance that the diaphragm must achieve in terms of service life and acceptable mechanical stresses.
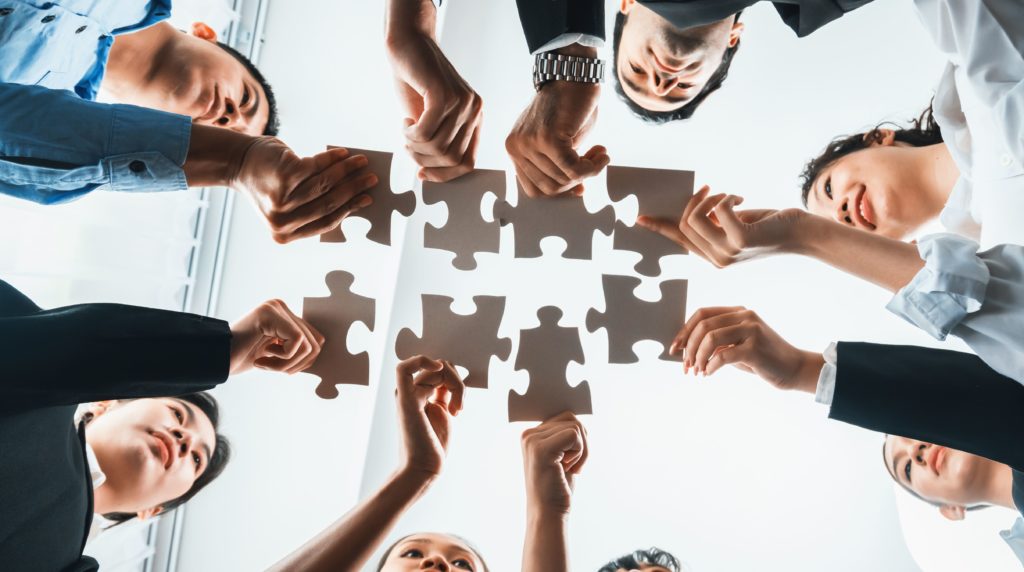
DRAW UP YOUR SPECIFICATIONS
From the design phase of your device, EFFBE engineers work with your teams to understand every dimension of your application (functionality, costs, performance, time-to-market, feasibility and desired endurance). They should also include all the factors likely to affect the performance of your equipment.
The main points to consider are:
- pressure differences
- extreme temperatures
- frequencies and harmonics
- service life and number of cycles
- the geometry and volume available
- the types of surrounding materials and how they are obtained
- the maximum stroke required
- integration / mountability in the device. EFFBE can advise you on the design of the surrounding parts.
- the cost
As a result of these discussions, a set of validated specifications is defined.

SELECT THE DESIGN AND MATERIAL OF YOUR DIAPHRAGM
Our Research&Development Department will create one or more designs for your rubber diaphragm, adapted to your pre-approved specifications. Its design work is based both on the use of our modelling tools and the quality of our feedback.
When developing a new application, our team uses analytical simulation tools to provide a predictive overview of the expected functional performance of your diaphragm. This predictive phase has the enormous advantage of improving the performance of your diaphragm and speeding up the time-to-market for your equipment.
Please note that we use SolidWorks for:
- fluid dynamics modelling,
- finite element calculations, non-linear finite element analysis, simulation of elastomer flow in mould cavities.
We also call on our Materials laboratory, which is constantly developing new formulations for the most demanding applications. It also anticipates future standards and regulations.
Right from the start of your project development, working together enables us to bring a wealth of added value to your diaphragm. If you want to comply fully with the specific standards of your different markets, or if you want the best possible response to the functionality and feasibility requirements of your equipment, don’t hesitate to call on our expert know-how.
At the end of this design phase, you validate the choice of material and the design of the part on the basis of the 3D drawings supplied by us.
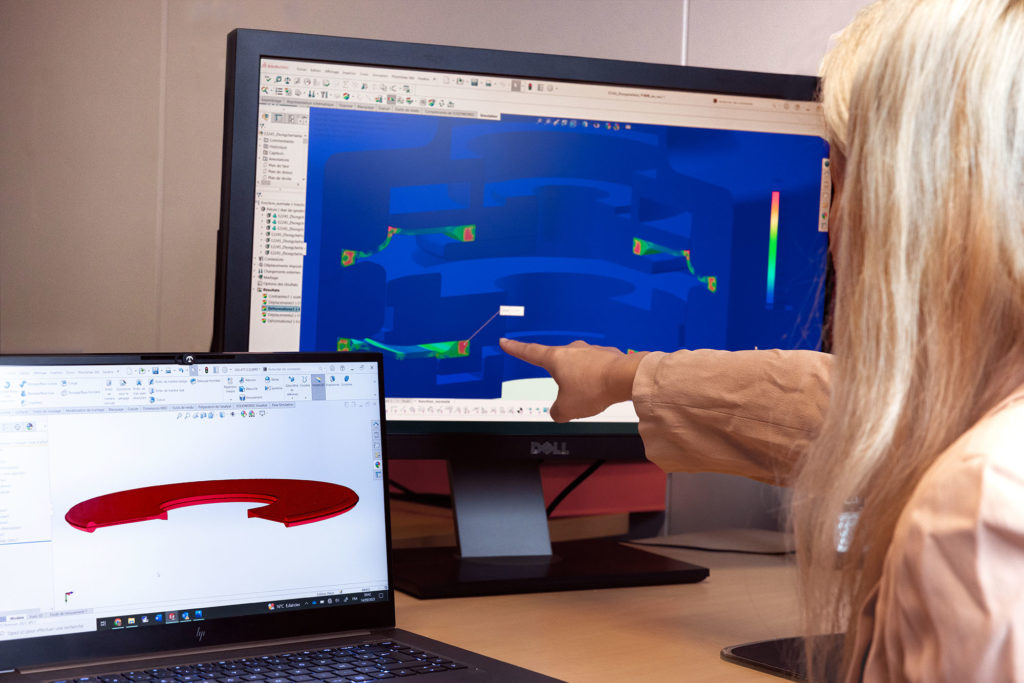
PROTOTYPE YOUR DIAPHRAGM
EFFBE designs the prototype moulds for your diaphragm. They are made by turning, milling or other traditional machining, either at EFFBE’s 3D machining centre – a solution that considerably reduces lead times – or at an approved partner.
3D printing is available from EFFBE for plastic parts. Some parts, particularly in silicone, can be produced by our approved 3D rapid prototyping partners.
Please note : prototype parts are always checked by our Metrology Department, which draws up a report for you.
The Metrology Department carries out its tests using the following methods adapted to the specific characteristics of our parts:
- an optical 3D measuring machine
- an optical measuring machine
- a low-pressure vertical meter
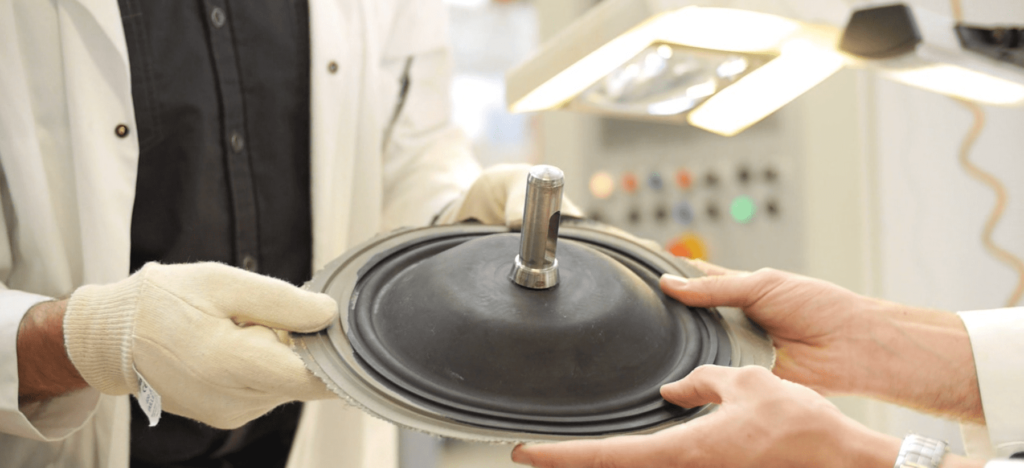
Do you have any questions?
We’ve got answers!
TEST THE PROTOTYPES TO VALIDATE YOUR FUTURE DIAPHRAGM
EFFBE can support and advise you in defining the best test protocols and the characteristics of the most appropriate test bench.
Chemical and mechanical tests can also be carried out at your request by us or our partners. This is why we carry out tensile, compression and other tests on your diaphragm, in accordance with the standards and norms in force.
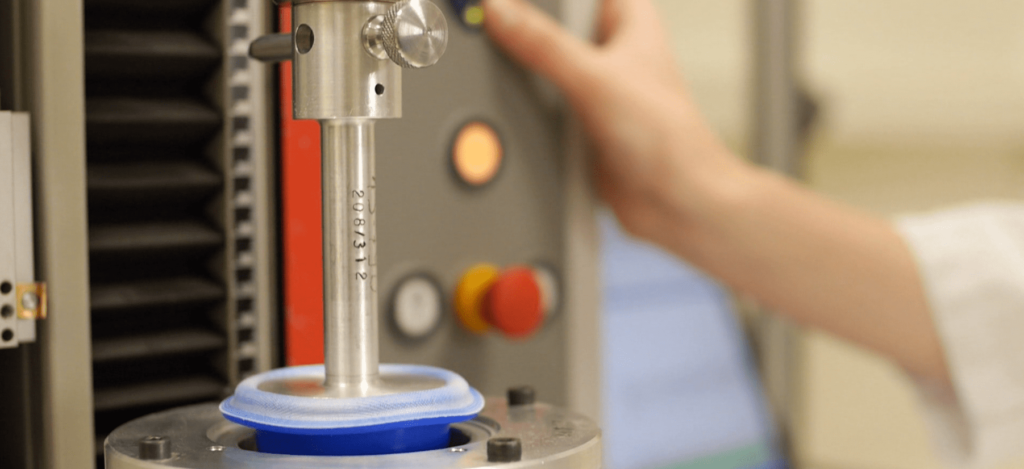
VALIDATE AND MANUFACTURE YOUR DIAPHRAGM
After a joint analysis of the performance of the prototypes, EFFBE’s Design Office may suggest adjustments to your diaphragm or even its surrounding parts. After your final approval, EFFBE manufactures your production tools. They will be the guarantors of the quality of your diaphragms and their dimensional compliance.
At the same time, we organise dedicated quality control for your diaphragm production, accompanied, if necessary, by a PPAP file including in particular:
- the different levels of risk and requirements: 1 to 5
- completing product and process risk analyses by checking that the preventive and corrective actions identified upstream have been implemented.
- presentation and validation of the process
- setting up a monitoring plan to ensure product compliance with customer requirements.
- initiating the defect palette that will follow the life of the product during series production
- material validation tests and reports
- dimensional validation of the product (dimensional reports as well as the results of machine and process capability reports)
- supply chain validation (packaging / flow management, etc.)
- validation of measurement means and methods relating to specific products (fitting / template / MSA)
Our project management methodology enables us to integrate your product requirements perfectly, whatever your industrial sector: automotive, aeronautics, nuclear, gas, medical, irrigation or other.
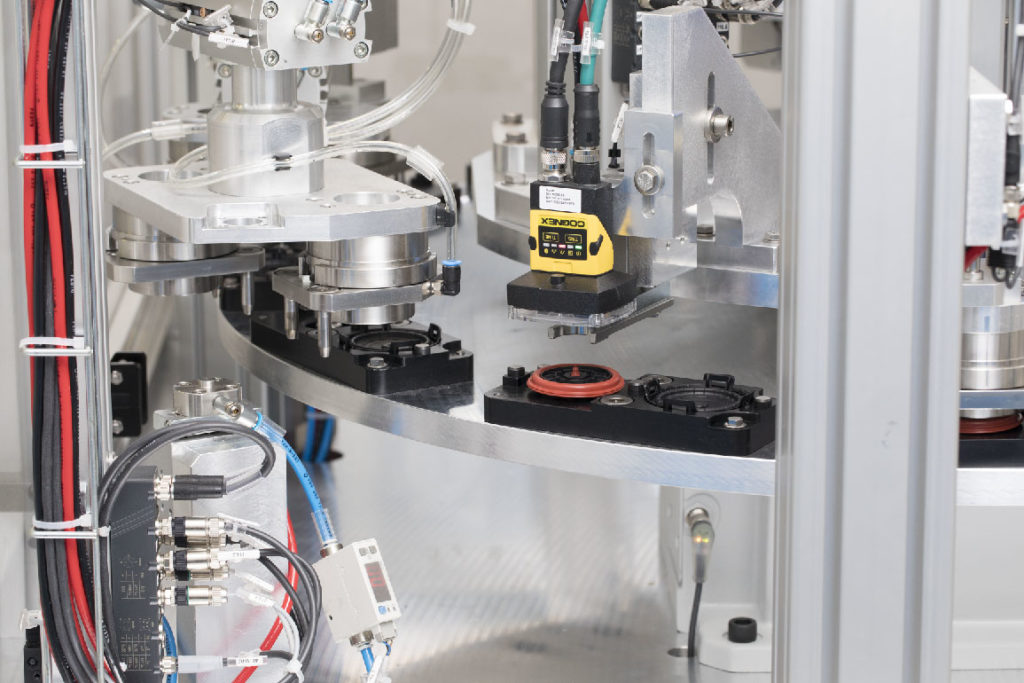
MASS-PRODUCE YOUR DIAPHRAGMS, ASSEMBLE THEM AND COORDINATE YOUR LAUNCHES
The mass-produced parts will be made on perfectly adapted presses and deployed identically at all our production plants. EFFBE has a comprehensive and competitive range of cutting, injection, transfer and compression presses.
If required, EFFBE uses specially developed, dedicated lines to assemble and mount sub-assemblies comprising the diaphragms and their surrounding parts, such as covers, cups, plates and inserts.
The assembled sub-assemblies are monitored by cameras at various stages of production. Specific checks are carried out on leak tightness and dimensions.
If you wish, EFFBE can also develop the packaging for your diaphragms, taking into account the environmental aspect. This is why we develop packaging that is as compact, light and ergonomic as possible, so that your diaphragms can be transported safely from their production plant to your workshops.
We offer a range of packaging solutions to suit your needs:
- bulck
- in Galia-type packaging
- on rolls
- in special blister packs designed on a case-by-case basis for ergonomic use at your workstations
EFFBE has production facilities on 3 continents to meet the requirements of each market and reduce the carbon footprint of your project through avoiding unnecessary, costly & polluting transport. With the same logic in mind, the selection of our global suppliers for our projects gives priority to their proximity to the selected production plants.
EFFBE’s Logistics Department will work with you to find the most cost-effective solutions for delivering your diaphragms on time. At your request, it can adapt to your INCOTERMS, including chartering carriers or handling customs declaration formalities.
Finally, our ERP can interface with your traditional or paperless ordering system. The same applies to your invoicing management system.
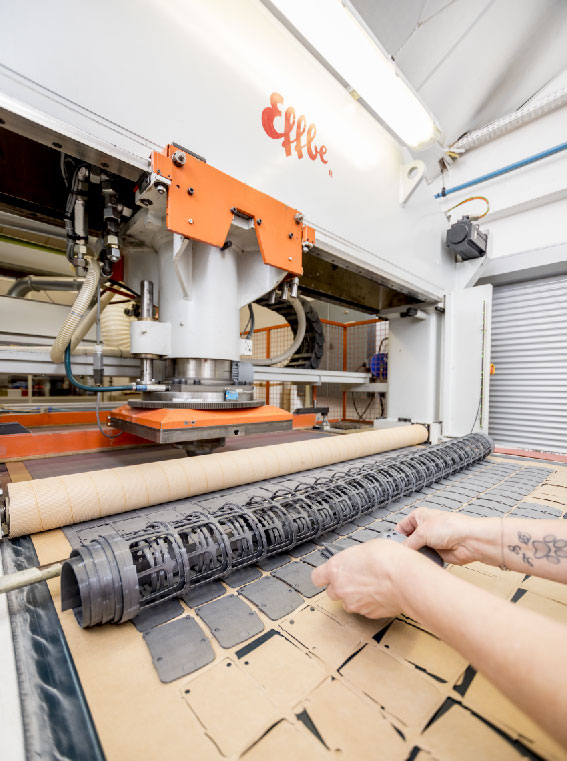
Do you have a project?
EFFBE engineers study all diaphragm development projects. Do not hesitate to contact us!